Backlog Commodity Reviews: Think Twice Before You Buy
- Waylin Frable
- Jul 15, 2023
- 2 min read
In today's fast-paced business world, maintaining efficient inventory management practices is crucial for the success of any organization. One important aspect of inventory management is conducting regular commodity reviews to assess the performance and value of items in a backlog. A backlog commodity review involves evaluating the inventory backlog to determine the status, condition, and relevance of the commodities. In this article, we will delve into the importance of backlog commodity reviews and provide a detailed guide on how to conduct them effectively.
Why Conduct Backlog Commodity Reviews?
Inventory Optimization Backlog commodity reviews help optimize inventory levels by identifying excess or obsolete items that may be tying up valuable resources. By eliminating such items, organizations can free up storage space and reduce carrying costs.
Financial Efficiency Reviewing backlog commodities enables businesses to identify potential financial risks associated with slow-moving or obsolete inventory. By addressing these issues promptly, organizations can minimize losses and maximize profitability.
Demand Forecasting Analyzing the performance of backlog commodities can provide valuable insights into customer demand patterns and trends. This information can help organizations refine their forecasting models and make informed decisions regarding inventory replenishment.
Strategic Decision-Making Backlog commodity reviews allow businesses to make strategic decisions about pricing, promotions, or inventory liquidation. By understanding the value and potential of each commodity, organizations can align their strategies with market conditions and customer preferences.
Steps to Conduct Backlog Commodity Reviews
Data Collection Gather relevant information about the commodities in the backlog, including purchase history, sales data, customer feedback, and market trends. This data will form the foundation for the review process. Categorization Categorize the commodities based on criteria such as sales volume, profitability, shelf life, or demand variability. This step helps identify priority items for review and analysis. Performance Assessment Evaluate each commodity's performance using metrics like inventory turnover ratio, gross margin, or sales velocity. Identify items with low turnover, declining sales, or deteriorating profitability. Market Analysis: Conduct a thorough market analysis to determine the external factors influencing each commodity's performance. Consider aspects such as changes in customer preferences, emerging trends, or competitive landscape shifts. Risk Identification Identify potential risks associated with each commodity, such as expiration dates, technological obsolescence, or regulatory changes. Assess the financial impact and determine appropriate actions to mitigate these risks.
Decision-Making Based on the analysis and risk assessment, make informed decisions about each commodity. This may involve restocking, discounting, bundling, or liquidating certain items, depending on their viability and market demand. Documentation and Communication Document the findings, decisions, and actions taken during the backlog commodity review process. Communicate the outcomes with relevant stakeholders, including inventory managers, sales teams, and procurement departments. Follow-up and Monitoring Regularly monitor the progress of the implemented actions and measure their impact on inventory performance. Adjust strategies as needed to maintain optimal inventory levels and mitigate future backlog issues.
For More Info: https://fortyreviews.com/backlog-commodity-reviews/
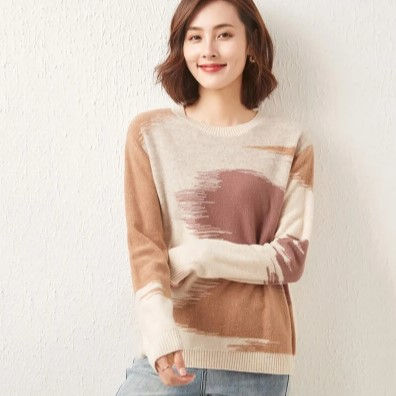
Comments